Dry Ice Blasting
- Meghan McCarthy
- Jul 26, 2023
- 2 min read
MacGas Dry Ice rice is ideal for dry ice blasting.
Dry ice blasting, also known as CO2 blasting or dry ice cleaning, is a non-abrasive and environmentally friendly cleaning process used to remove surface contaminants, coatings, or debris from various materials and equipment. It employs dry ice, which is the solid form of carbon dioxide (CO2) at extremely low temperatures (-78.5°C or -109.3°F), as the blasting media.
The process involves the following steps:
Dry Ice Production: Liquid carbon dioxide is pressurized and then released to expand into a gas. The gas is then condensed into solid dry ice pellets or blocks.
Blasting Equipment: Specialized dry ice blasting equipment is used, which typically consists of a blasting gun or nozzle and an air compressor. The dry ice pellets are loaded into the equipment's hopper.
Blasting Process: Compressed air is used to propel the dry ice pellets at high speeds towards the surface that needs to be cleaned. When the pellets impact the surface, they immediately sublimate (convert from solid to gas), creating a rapid temperature change.
Contaminant Removal: The combination of kinetic energy from the blasting and the extreme cold temperatures causes the contaminants, such as dirt, grease, paint, or other unwanted materials, to loosen and break away from the surface. The force of the sublimation also helps lift the debris away.
Environmental Safety: Dry ice blasting is considered environmentally friendly because the CO2 used is a byproduct of other industrial processes, and the blasting process itself doesn't generate any secondary waste. It doesn't produce harmful chemicals or contribute to greenhouse gas emissions.
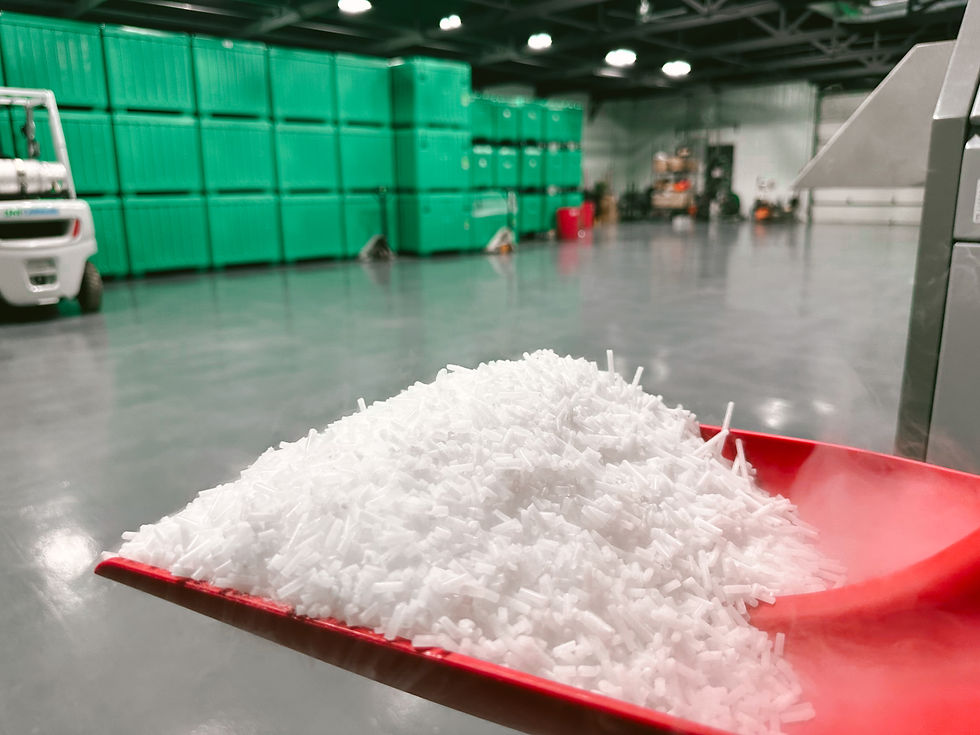
Dry ice blasting is effective in a wide range of applications, including industrial cleaning, mold remediation, paint and varnish removal, fire damage restoration, and equipment maintenance. It is a popular choice in industries like manufacturing, food processing, aerospace, automotive, and more, where traditional cleaning methods might be unsuitable due to the generation of waste or potential damage to sensitive equipment or surfaces. Additionally, the process is non-conductive, making it suitable for electrical equipment cleaning without the risk of electrical shock.
Comments